Aluzinc and Aluminum are two common metallic materials used in construction, industry, agriculture, automotive, electronics, transportation, etc. Both include aluminum in their composition, and each has its advantages and applications. Wanzhi Group will introduce you to these two materials in terms of composition, process, performance, application, and characteristics.
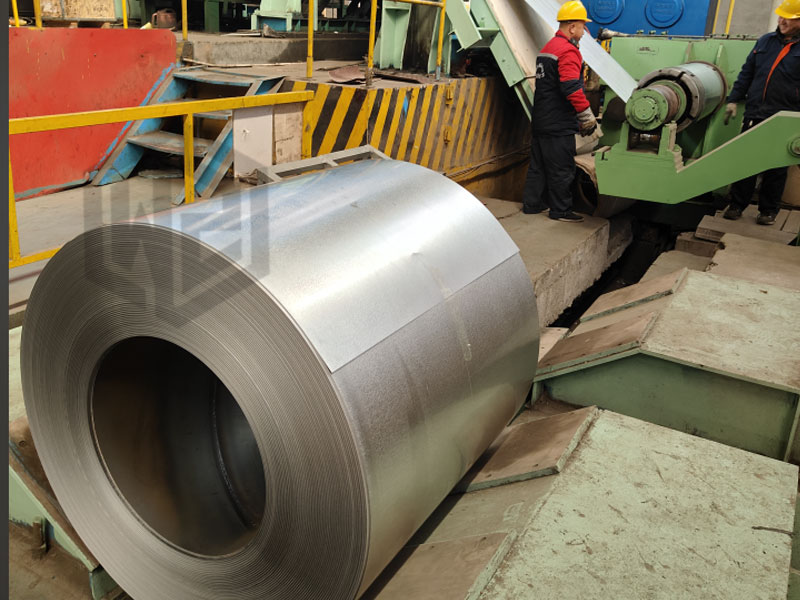
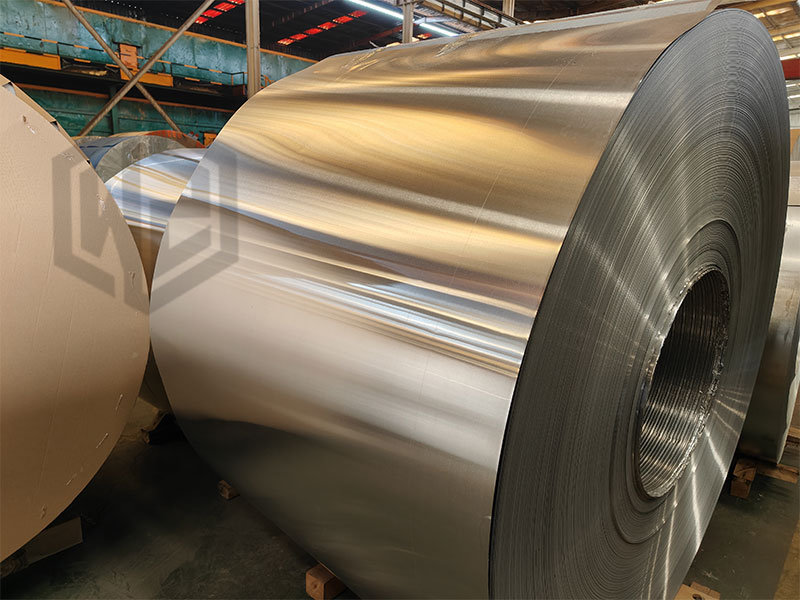
What are Aluzinc and Aluminum?
Aluzinc and Aluminum are two metal materials commonly used in construction, manufacturing, and industrial applications. Aluzinc steel is an alloy-coated steel and aluminum is a lightweight metal.
Aluzinc (aluminum-zinc coated steel sheet)
Composition: 55% aluminum + 43.4% zinc + 1.6% silicon alloy coating over mild steel substrate (e.g. DX51D).
Characteristics: Combines the strength of steel with the corrosion resistance of an aluminum-zinc alloy, making it suitable for harsh outdoor environments.
Aluminum (Aluminum and Aluminum Alloys)
Ingredients: Pure aluminum (Al≥99%) or alloys with added copper, magnesium, and silicon (e.g. 6061-T6, 3003-H14).
Characteristics: Lightweight, high thermal and electrical conductivity, suitable for weight reduction and precision processing.
Aluzinc, Aluminum Composition, and Production Process Comparison
Comparison Item | Aluzinc | Aluminum |
---|---|---|
Substrate/Alloy Type | Mild Steel (SPHC, S350GD, etc.) | Pure Aluminum or Aluminum Alloys (1xxx-7xxx series) |
Coating/Alloy Composition | 55% Al, 43.4% Zn, 1.6% Si | Pure Aluminum (Al ≥ 99%) or with Cu/Mg/Si, etc. |
Production process | Hot-dip aluminum-zinc plating (600-620°C) | Electrolytic smelting → rolling/extrusion/casting |
Density | 7.85 g/cm³ (steel substrate + plating) | 2.7 g/cm³ (only 1/3 of steel) |
Aluzinc, Aluminum Mechanical Properties
Properties | Aluzinc | Aluminum |
---|---|---|
Tensile Strength (Rm) | 270-550 MPa | 70-500 MPa |
Yield Strength (Rp0.2) | 140-350 MPa | 30-450 MPa (e.g. 6061-T6 up to 276 MPa) |
Elongation (A50) | 14-25% (the thinner the substrate, the higher the elongation) | 10-25% (higher for pure aluminum, lower for high-strength alloys) |
Hardness (HV) | 100-160 HV | 20-150 HV |
Modulus of elasticity | 200-210 GPa | 69-73 GPa |
Fatigue strength | 150-250 MPa | 50-150 MPa |
Comparison of properties of Aluzinc and Aluminum
Properties | Aluzinc | Aluminum |
---|---|---|
Corrosion Resistance | ⭐⭐⭐⭐⭐
(salt spray life 1500–3000 hrs) |
⭐⭐⭐⭐
(pitting susceptible, dependent on surface treatment) |
Tensile Strength | 270-550 MPa (substrate dependent) | 70-500 MPa (alloy type has large effect) |
High Temperature Resistance | ≤ 315°C (long-term stable) | ≤ 660°C (pure aluminum) Melting point, alloys can be higher) |
Thermal conductivity | 50 W/m-K (steel substrate) | 237 W/m-K (pure aluminum, better heat dissipation) |
Machinability | special tools required for cutting, cold bending radius ≥ 1x plate thickness | easy to cut, bend, weld (especially thin plates) |
Cost | steel substrate + plating | depending on the alloy type |
Application Scenarios for Aluzinc and Aluminum
Aluzinc steel is widely used in outdoor and industrial applications for high corrosion resistance and strength, while aluminum is widely used in lightweight, easy-to-machine precision and weight reduction applications.
Application Scenarios | Aluzinc | Aluminum |
---|---|---|
Construction Industry | Industrial plants, coastal buildings, warehouse beams, bridge parapets, noise barriers | High-end curtain walls, decorative facades, canopies, sunshades, thermal insulation windows |
Automotive & Transportation | Exhausts, chassis guards | Electric vehicle bodies, battery housings, dashboard brackets, door frames, aircraft fuselages, boat hulls |
Electronics & Home Appliances | Air conditioners, oven housings, electrical control cabinets, transformers housing | Cell phone/laptop housing, CPU cooler, LED lampshade |
Agriculture and Industry | Grain silo, chemical plant, reactor tank shell, pipe supports, solar energy bracket | Ventilation ducts, light distributed photovoltaic |
Comparison of Aluzinc and Aluminum Advantages
Aluzinc steel coil and sheet have the characteristics of salt spray resistance, typhoon resistance, and high load bearing. Reflect 80% of the sun’s heat, high temperature, rust, weather resistance, conductive, ammonia, acid and alkali resistance, high strength support, etc. Aluminum is lightweight and aesthetically pleasing, low thermal conductivity, good thermal insulation, is easy to mold, aesthetically pleasing, energy saving, lightweight + seawater resistance, precision machining + heat dissipation, thermal conductivity of 237W/m-K, and so on.
Advantages of Aluzinc
- High thermal reflectivity: Suitable for energy-efficient buildings.
- High corrosion resistance: Aluminum provides oxidation resistance and zinc provides sacrificial anode protection, preferred for coastal/industrial areas.
- High strength: Aluzinc is stronger than aluminum due to its steel base material.
- Moderate weight: heavier than pure aluminum, but still lighter than pure steel.
- Appearance: The surface is usually a silvery gray with a glossy finish.
- Economical: Costs less than stainless steel.
Advantages of Aluminum
- Lightweight: Aluminum is lighter than most metals, shedding 30-50% of its weight.
- Good corrosion resistance: Aluminum naturally forms an oxide film on its surface, which prevents further oxidation.
- Good electrical and thermal conductivity: Aluminum is an excellent electrical and thermal conductor.
- Highly malleable: Aluminum is very easy to work with and form, suitable for complex designs, and can be cast and formed in a variety of ways.
- 100% recyclable: environmental advantages
Environmental Protection and Sustainability of Aluzinc and Aluminum
Indicators | Aluzinc | Aluminum |
---|---|---|
Recycling rate | 80-90% for steel substrate, difficult to separate plating | 95%+ recoverable, low recycling cost |
Carbon emissions | Higher energy consumption for production (plating process) | High energy consumption for electrolytic aluminum, but 95% less energy for recycling |
Environmental certifications | RoHS (Chrome Free Passivation) | LEED (Green Building Points) LEED (Green Building Plus) |
Frequently Asked Questions
Q1: Which is better, Aluzinc or galvanized steel (GI)?
Aluzinc is more corrosion resistant (lasts 3–6 times longer than galvanized steel), but costs 20-30% more.
Q2: Can aluminum alloy be used for roofing instead of Aluzinc?
Yes, but you need to choose a high-strength alloy (e.g. 5052-H32) and the cost is 3-5 times higher.
Q3: Which material is more suitable for the food industry?
Aluminum (easy to clean, non-toxic), but needs a surface coating to prevent corrosion.
Hot Products
Depending on your project needs, choose the more cost-effective metal material, aluzinc steel for high strength + corrosion resistant projects, or aluminum/premium aluminum for lightweight + complex molding, contact Wanzhi Group for a price list!